What is a Box Build Assembly?
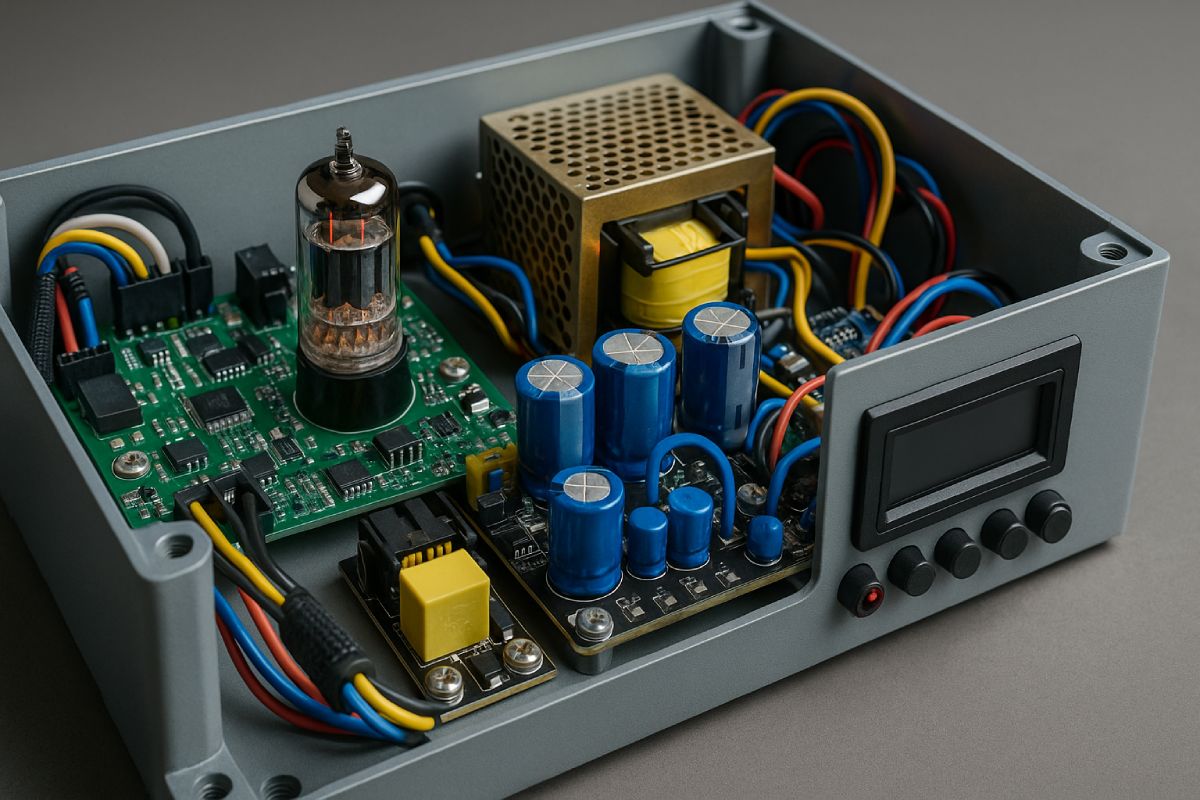
- Introduction
- Key Takeaways
- What is a Box Build Assembly?
- Where are Box Build Assemblies Used?
- Key Components of a Box Build Assembly
- The Box Build Assembly Process
- The Challenges in Box Build Assembly
- How to Choose the Right Box Build Assembly Partner
Introduction
A box build assembly is an electronic assembly in which all the components are assembled inside of an enclosure (the box). They are manufactured as a single unit that either is a final product itself, or which can be integrated into a final product. Box build assemblies can be composed of various components, including printed circuit boards, cables and other electronic, electrical and mechanical components.
In this article, we’ll explain what box build assemblies are, we’ll talk in detail about the components that typically comprise a box build assembly, how manufacturing and assembly processes work and what applications box build assemblies are typically used in.
Key Takeaways
- Box build assemblies are used across a huge number of industries
- The box build assembly is complex and requires a diverse skillset from the manufacturer, everything from mechanical to electromechanical assembly experience
- It’s important to consider how designs will affect the cost and complexity of producing the assembly
Table of Contents
What is a Box Build Assembly?
Box build assembly fabrication is the process of assembling multiple components to form a finished product or system that is contained within an enclosure. Completing a box build assembly involves adding components, mounting them, integrating wiring and installing sub-assemblies. Box build assemblies also need to complete final tests and inspections before they can be used.
Box build assembly is often referred to in industry to as system integration.
Unlike PCBAs, box build assemblies are built as complete and finished systems, ready for use. Box build assemblies are often built by specialist manufacturers with established procurement networks and experience in all stages of box build assembly production.
Where are Box Build Assemblies Used?
Box build assemblies are used in a huge range of products and in all industries. They can be used in any product that requires the integration of electrical, electronic, mechanical, electromechanical and software components into a single unit. They can also be built to a wide range of sizes, from different materials and with many different functions.
Here are some products that are often built with box build assemblies:
- IoT devices: Smart home devices, industrial devices and other IoT devices can be built with box build assemblies.
- Medical devices: Box build assemblies are used in medical devices such as diagnostic equipment, patient monitoring systems and surgical tools.
- Consumer electronics: Smartphones are a well-known example of a box build assembly. They’s also used in tablets, laptops and other electronic devices.
- Industrial equipment: Industrial equipment such as machinery control systems, automation systems and monitoring equipment.
- Automotive products: Automotive products such as navigation systems, ECUs and entertainment systems.
Key Components of a Box Build Assembly
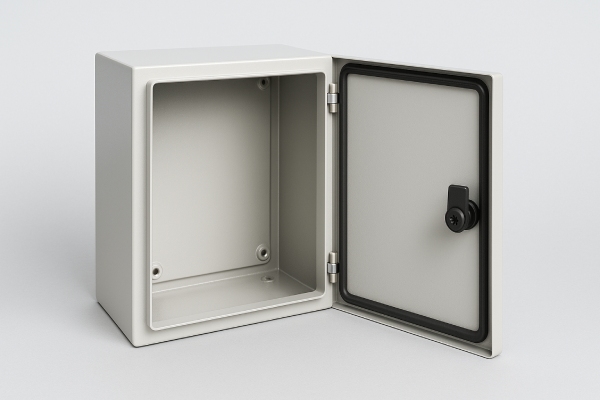
Box Build Enclosure
Enclosures are typically made from metal or plastic, which can be sheet metal, injected plastic, stamped, formed, etc.
Metal enclosures are physically stronger and can often be manufactured without needing any tooling in production or with very limited tooling.
- Sheet metal enclosures if not tooled require low upfront costs, and it makes modification easy.
- metal enclosures have a higher per unit part cost
- There are more limitations to size, shape and configurability
- Sheet metal enclosures can be more costly and complex to waterproof
Plastic enclosures are cost effective, low weight, easier to waterproof and resistant to corrosion.
- Unless you use an off the shelf enclosure, they generally require tooling to manufacture.
- Tooling requires higher upfront costs and longer manufacturing time.
- Plastic enclosures also have poorer resistance to UV exposure and physical impact or damage.
Printed Circuit Board (PCB)
Printed circuit boards are a key component of box build assemblies. A box build assembly manufacturer will produce a printed circuit board assembly (PCBA) for inclusion in the final box build assembly.
This is a printed circuit board (PCB) that has been fully assembled with all required electronic components for in-use operation. The box build manufacturer may produce their own PCB or outsource it.
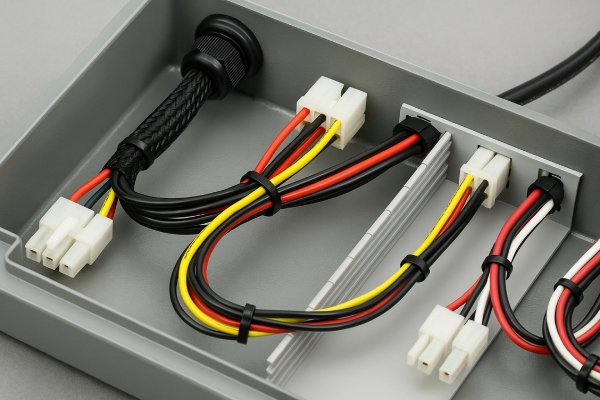
Cable Assemblies and Wiring Harnesses
Cable assemblies and wiring harnesses are crucial for connecting all the different electrical and electronic components of a box build assembly together.
Cable assemblies and wiring harnesses have to be well designed for good final functionality. Here are some important considerations:
- Wires should be secured and appropriately routed with wire ducts, strain reliefs and other mounting components.
- Connector positions should simplify cable routing.
- Wires should have support at points at which they enter the enclosure.
- Waterproof enclosures require secondary sealing or IP rated waterproof cables.
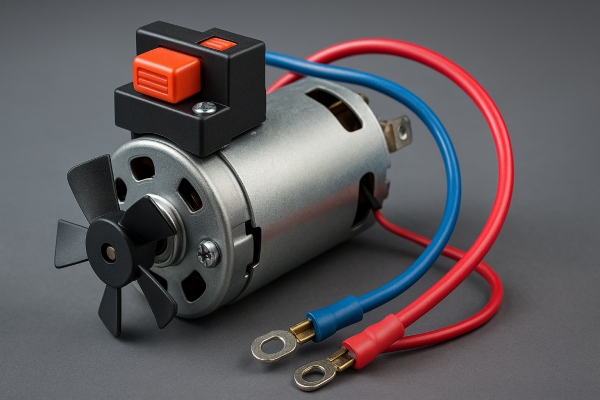
Electromechanical Components
Box build assemblies can include a huge range of electromechanical components. These can be components that provide an interactive function to the end user. Otherwise, they can be components that operate in the background to regulate the device itself.
Here are some examples of box build assembly electromechanical components:
- Fans
- Motors
- Buttons and switches
- LED indicators
- Electrical sensors
- Actuators
- Displays
Manufacturers need to make a number of considerations when incorporating electromechanical components in box build assemblies. Some of the important considerations are space constraints, cable routing and strain relief, power requirements, heat distribution and integration with other components.
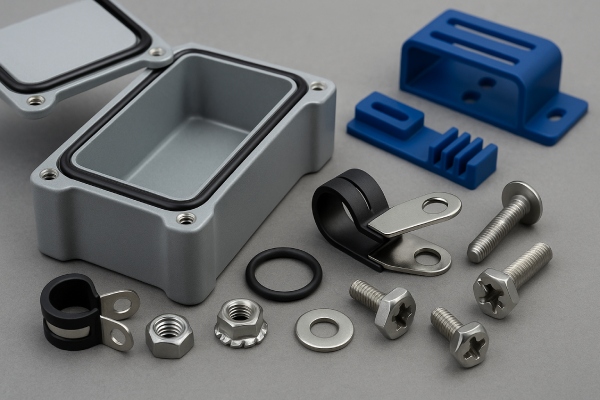
Mechanical Components
Box build assemblies feature hardware and other mechanical components that form part of the structure of the unit. These can be to add security, structural support or waterproofing, for example. Otherwise, they might provide a function, such as an opening and closing lid.
Here are some common mechanical components:
- Lids and hinges.
- Fasteners – Such as tamperproof nuts for security or lock washers for vibration proofing.
- Gaskets for waterproofing or other sealing purposes.
- Cable mounts and cable organizers.
There are various design considerations when choosing mechanical components. The type and material are major considerations, but there are also many other possible design considerations.
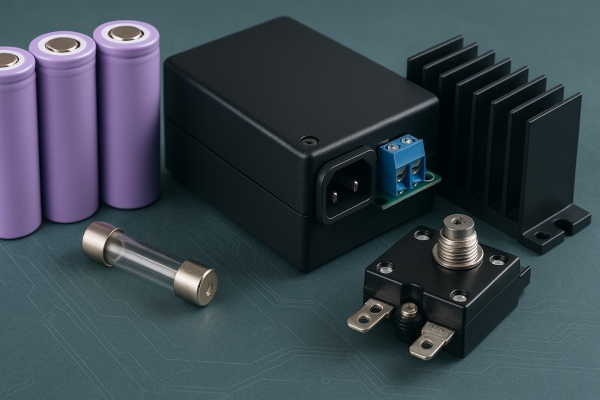
Power Components
Box build assemblies always require power components, whether they are powered by batteries or from a fixed power supply. Power components require appropriate housing and connecting components. They might also require other ancillary components. Overcurrent protection and thermal management are important safety considerations.
There are often regulatory requirements that have to be met when it comes to power components in box build assemblies. Some regulatory requirements are simple, but there can also be more complicated requirements. Examples include component level certification (such as UL/UN certification for batteries) or electromagnetic compatibility (EMC) testing for emitted radiation.
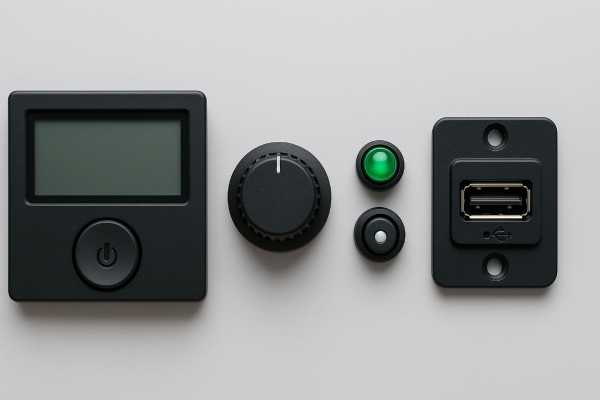
User Interface
Box build assemblies may or may not require a user interface. This might be control features, such as buttons or a touch-screen display. Alternatively, there might be indicators, such as LED lights or an LCD display screen, or connectivity features, such as Bluetooth or a USB port.
Here are some examples of user interface features on box build assemblies:
Buttons, switches and dials.
- USB or ethernet connector ports.
- LCD display screens.
- LED indicator lights.
- Rocker switches.
- Mechanical or membrane keypads.
The Box Build Assembly Process
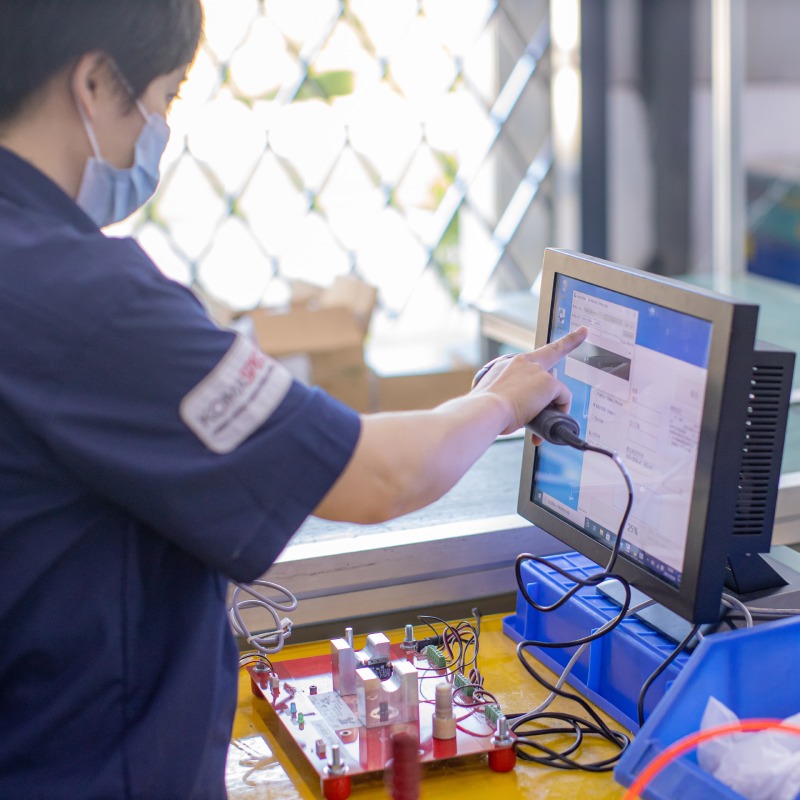
Box build assembly manufacture is complicated. Manufacturers need to have good knowledge of manufacturing processes and be able to plan complicated component sourcing and assembly processes. A number of steps need to be undertaken, and the entire operation needs to be well sequenced for efficient and successful manufacture.
Here are the steps in box build assembly:
1. Design and planning
Designs specifications should be clearly defined, and they should also be analyzed for possibilities to make manufacturability improvements to design. Usually there are improvements that can be made in by simplifying the assembly process, combining sub-systems or reducing enclosure complexity. Designs then need to be converted into detailed assembly instructions.
2. Component procurement
Supply chain management is a big task in box build assembly. Many parts need to be sourced, and they might need to be delivered sequentially during production or held in storage. If there are many components (e.g. dozens) or if there are difficult to procure PCBA-level components, it becomes much more difficult to procure parts at the right time and manage production.
3. Mechanical assembly
The assembly enclosure and any mechanical structures will need to be fabricated. This may require specialist sheet metal or plastic manufacturing processes. After this, components have to be physically mounted inside the enclosure with screws, zip ties, glue, rivets or by other methods.
4. Electrical assembly
PCBAs should be manufactured along with cable assemblies, electromechanical parts and power supplies. Then they need to be connected via cables and leads to complete the box build’s electrical system.
5. Software and firmware installation
If any software or firmware is included, this will need to be installed by connecting to the PCBA. This stage can also be combined with PCBA testing so that the manufacturer can complete quality testing for the PCBA at the same time.
6. Testing and quality assurance
Testing and quality assurance are not straightforward with box build assemblies because there are so many components and performance considerations. Generally, there needs to be a layered approach, with initial testing and qualification of component suppliers and batch testing of incoming components. After this, on-line or end-of-line functional testing can be used to ensure the system works as designed. Custom testing jigs, such as PCBA flashing and testing fixtures, can also be built into the assembly process.
7. Packaging and shipping
Packaging should be secure to keep electrical and other delicate components safe during transit. Proper documentation and labeling should also be provided.
The Challenges in Box Build Assembly
Box build assembly can be anything from straightforward to extremely complex. Some IoT enclosures are built with little more than a PCBA and a few cables. At the other end of the spectrum, you have box build assemblies that features an electrical enclosure with 50-60 components and dozens of cables.
More complex builds require a long list of capabilities on behalf of the manufacturer:
- Good control over sourcing, procurement and quality control of passive components or electrical components from a range of suppliers (motors, fans, cables, heat sinks, PCBAs, etc.).
- Extensive assembly capabilities, covering manufacturing processes such as potting, ultrasonic welding, soldering and enclosure fabrication.
- Engineering capability to debug and troubleshoot design or quality issues.
Importantly, good box build assembly requires good supply connections and good supply chain management. Established manufacturers have an advantage because they have established specialist supply networks, the facilities to manage supply inventories and experience dealing with complicated supply operations.
Good box build assembly also takes the ability to complete complicated assembly processes and specialist manufacturing processes. Not only are some fabrication processes complicated, but different processes in mechanical and electrical manufacture have to be aligned with each other in the manufacturing process. This takes good fabrication schedule management.
Testing and quality control is also crucial in box build assembly, with both processes often needing to be completed at various stages. Testing and quality control processes can also be complicated. Complicated electrical components may need to be tested for functionality, for example.
How to Choose the Right Box Build Assembly Partner
As we mentioned at the start, most companies outsource box build assembly fabrication to specialist companies. The process is difficult to manage in-house, and specialist companies can usually complete work to a higher standard and for a lower price.
If you are looking for a good box build assembly partner, here are some of the important things to look for:
- A complete end-to-end service
- Cost competitiveness
- Acceptable lead times
- Extensive production skills
- Ability to work with customer consigned inventory
- Design and engineering support
- Production scale flexibility
- Good communication and customer service
Komaspec is a Canadian-owned manufacturing company with more than 20 years’ experience in a range of manufacturing disciplines. We provide a turnkey box build assembly manufacturing service and handle box build manufacturing projects for clients in a range of industries.