Design Tips for Stamping Parts with Progressive Dies
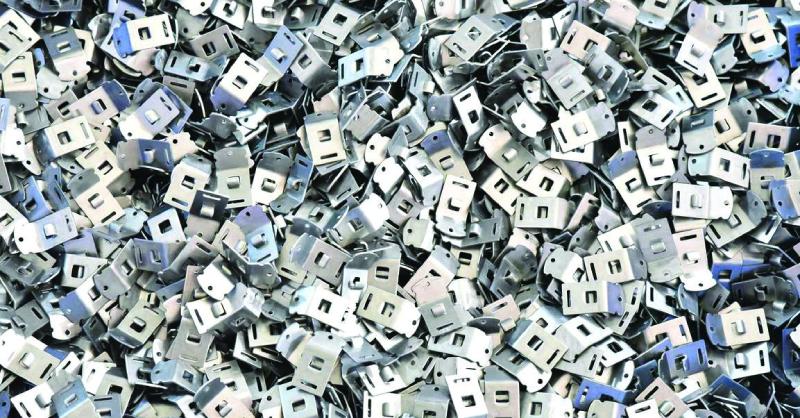
Progressive die stamping for sheet metal fabrication
Progressive die stamping for sheet metal fabrication is a complex process. For that reason, you want to design the tooling accurately in order to achieve the quality part you want.
We’ve included several design tips in this chapter to help you along the process.
Many of these factors are interconnected so decisions about each should be made concurrently, which can sometimes lead to trade-offs in your design and outcomes.
Several prototype runs are usually necessary to perfect the design before production.
Sequence design / strip layout
Your design will determining the sequence in which the part will be formed, including the number of forming processes and their corresponding dies.
This is a complex process and can present significant challenges so working with a designer who has experience in progressive stamping is an advantage.
- The strip layout can impact your costs, accuracy, and quality
- The sequence should be appropriate for the part and material thickness, the material properties, the desired surface finish, and other variables such as inconsistent source material thickness and work hardening
- Each step in the sequence requires specifications for the tooling, draw depth, or blank holder force
- Tooling should be designed to minimize weakening and to facilitate maintenance
- Empty stations can help minimize die weakening and to compensate for concerns about the drawing or movement of the strip
- Empty stations initially allow for the addition of operations at a later time
- When force across the strip is not distributed evenly, movement or tipping can occur when the press is engaged, causing damage to the dies which can impact consistency and quality across parts. Your sequence design should consider this factor.
- The part may need to be oriented on the strip at an angle to the grain in order to avoid cracking and fatiguing that sometimes occurs when forming with the grain. This is especially important if tight tolerances are necessary. There is more material waste in this case.
- Orient the part on the strip to have the shortest feed possible, especially when using heavy material with narrow strips. This helps the feed run easier and faster.
Order and track sheet metal components online through Komaspec's on-demand sheet metal fabrication platform.
Carrier / webs / strips / ties
The material that carries the parts through the progressive stamping dies is sometimes call the carrier, or webs, strips or ties.
It connects and transports the part to each die station. There are several different types of carriers that allow for different processes on the part.
- Designing the carrier within the width of the part minimizes the need for additional material to be included in the process
- Carrier width should be at least 2 times the material thickness
- Larger dies may require larger carrier widths to facilitate pushing the strip through the die
- If more than one carrier is used, try to design with consistent lengths to prevent twisting of the strip
- Design carriers long enough to accommodate any stretch or bend necessary during any of the press operations. These loops should be designed with as large a radius as possible but still allows for any necessary clearances
- Try to attach the carrier at a point that will allow it to be removed easily and any burrs that result can be addressed
- Use stiffening beads to carriers or lance form the edge when large parts are being fabricated from thin materials
CENTER CARRIERS
- Formed by a strip of metal near the center of the part
- Narrow center carriers allow for forming around the entire part
- Wide center carriers only allow for forming on the sides of the part
- Usually results in minimal scrap material
INBOARD CARRIERS
- Attached to the part at two points – one near the center and one near the outside of the part
- The carrier does not exceed past the width of the part
LANCE CARRIERS
- A lance is created instead of trimming material from the strip
- Minimizes scrap but creates shaving
OUTSIDE CARRIERS
- Attached to the outside of the part and formed by trimming, lancing, or punching shapes for drawing
- Allows for forming near the center of the strip
- Lifter rails are often used to feed and balance the strip
ONE-SIDED CARRIERS
- Attached to only one side of the part
- Allows for forming on three sides and maximizes access to the part for forming
- Can cause issues with movement when lifting and feeding the strip
- Usually requires lifters along the center of the strip to feed it through the dies
- Lift maybe difficult if several large flanges are formed downward
- Can be issues with alignment as significant excess material is trimmed around the part. To avoid this problem, increase the width of the strip so trimming can also occur on the side of the carrier.
Feed height and strip lifting
The feed height is defined as the amount the strip must be lifted to progress to the next die.
Even for flat pieces, slight lift is required to break the oil seal with the die.
Strip lifters are used to support the progression of the strip from die to die.
- Design with the minimal lift possible as lifting adds to the time required for part manufacturing
- The amount of lift should consider necessary clearance to prevent catching on the next die. Bending processes for example require the part to be lifted high enough to clear the die that created the bend
- The higher the lift height, the higher the chance it can impact the orientation of the strip from vibration or bounce
- Sagging between strip lifters can cause buckling to the carriers
- Spool lifters that are spaced too far apart can cause thin materials to not remain flat, affectingpilot positioning
- Bar lifters can run the distance between two parts, providing better support to thin materials and help prevent sagging
- Rotating the part on the strip so it’s at an angle to the grain can help reduce the lift required. If all the forms are in the same direction, the form can be made upward instead. This may have more costs for the die and materials.
Pilots
Pilots are very important to the progressive stamping process. They are what align and fix the strip into the correct position as it progresses through the machining.
The number of pilots and their location have an impact on the material and the carrier type you use.
- Parts that contain holes can use those holes as pilots, if they are large enough. If the hole is designed for tight tolerances, using it as a pilot can result in some elongation and imperfections
- Pilots spaced on the carrier can be designed to account for any elongation, so the part tolerances are achieved
- If two sets of pilots are required, punch both at the same time for better accuracy
Exiting the die
Special considerations come into play when designing how the final die will finish a part, including the orientation of the design on the strip, the carrier type, and the overall die sequence.
- Ladder strips are usually the easiest way to remove a part and may not require a die to be cut
- Shedder pins can be used to move the part off of the last die
- The sequence for heavier parts can be such that they are slightly off balance on the final die and will fall off
- Clearance is required for any downward forms or flanges so the part is removed from the die
- Flanges or forms designed upwards will often fall from the final die simply by the progress of the strip
The team of engineers at Komaspec have more than 20-year experience in sheet metal fabrication and both progressive and standard stamping processes in our China-based sheet metal facility, and are glad to provide a product consultation and detailed DFM feedback to best optimize your stamping tooling and part design by reducing cost and improving output where possible.
We are glad to review your product design together and help you select the fabrication process that best suits your product’s needs.